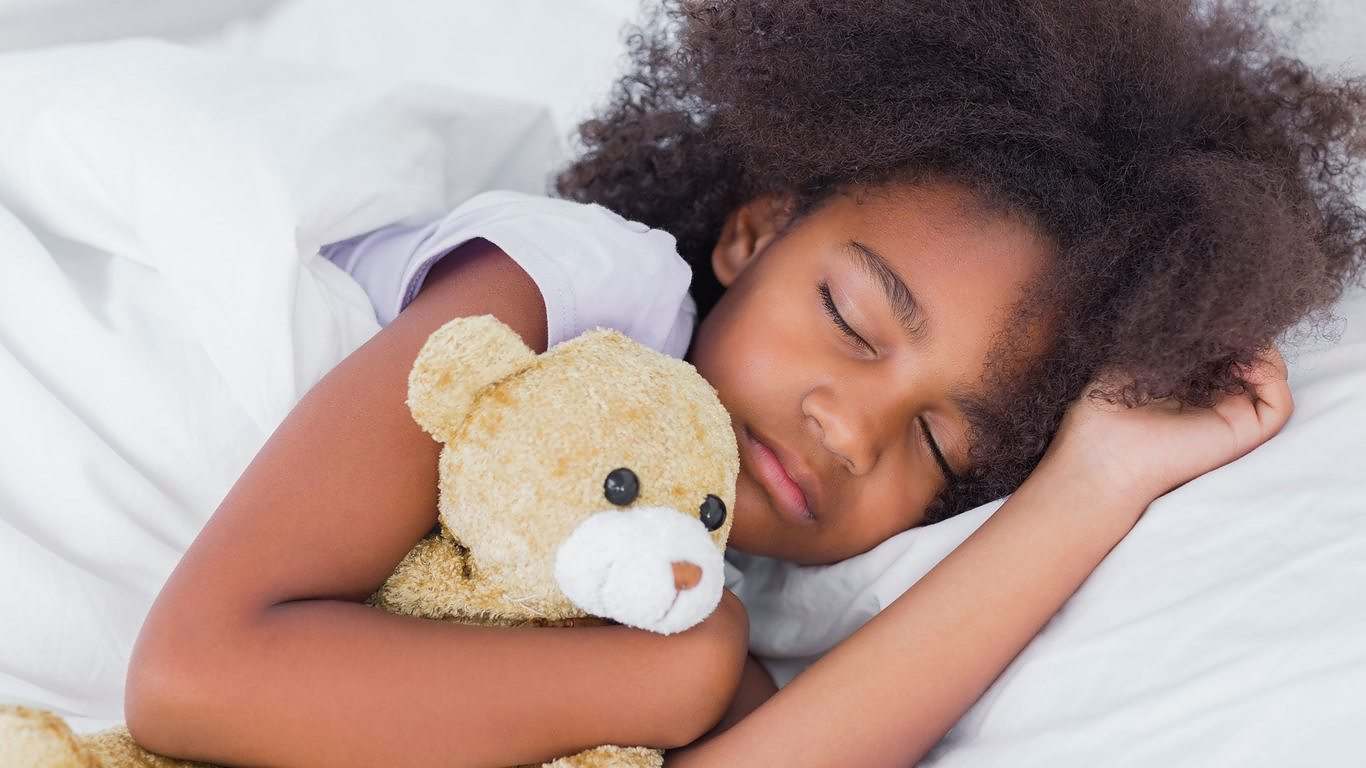
Avoiding Mold on Imported Products
Several clients have asked us of ways to avoid mold damage to products that they import into the Colon Free zone by container from a Chinese, Vietnamese, or Indian factory.
This is a serious problem and can cost the importer / distributor thousands of dollars in damages to goods.
The reason for the mold growth and resultant damage during trans oceanic container shipping is typically a combination of these factors;
- the products are contaminated with mold spores while in the factory, and/or
- the products are too wet when packed, and/or
- the packaging (cardboard boxes) are moist when shipped and/orthe wooden pallets used in the container are moist
- the air inside the shipping container has a high relative humidity (above 55%)
And what happens during the long transportation time period… mold matures and develops on the goods.
The mold growth problem gets much worse as the products arrive in Panama and are further handled and stored in the high relative humidity environment of receiving docks and warehouse spaces in the Colon Free Zone, which typically is 75% to 85% relative humidity or higher. Mold growth will start to become noticeable at 55% relative humidity, and growth rates accelerate by a factor of ten for every 10% increase in relative humidity.
Are there solutions for shipping?
Humidity in ocean containers from Asia has been a problem ever since there have been ocean containers, but there are some really effective ways to minimize and/or eliminate such issues, sometimes without the use of desiccants. Humidity is Colon Free Zone warehouses has also always been a problem. Most operators feel air conditioning is the answer, but careful consideration should be given to use of industrial grade dehumidifiers to bring sealed warehouse spaces down to an optimum 50% level.
Desiccants and effective use of them
First, though, you should know a little more about how desiccants work. Did you notice on the any of the desiccant manufacturer or supplier sites that their test data for effectiveness was based on a sealed chamber? A sealed chamber controls the exact amount of humidity/moisture available to the desiccant, while an ocean container is not airtight. Quite the opposite. As a result, it would be difficult/impossible for desiccant to really absorb all the moisture available in an ocean container or within the cardboard boxes that house the goods.
Also, when thinking of the volumetric space of an ocean container, one should remember that it’s possible to displace much of that volume by densely packing the container with products. Unfortunately, shoes are not very dense, nor is the package surrounding shoes. This type of product and packaging make for a worse case condition, but there are ways to mitigate the situation.
The most effective use of small packs of desiccants can be found on items like cameras that have tight-fitting packaging surrounding them. Some cameras use molded expanded polystyrene foam (EPS) that fully encapsulates the camera. By creating this kind of foam box, only a small amount of desiccant is needed to absorb moisture found in the cavity of that foam. If the shoe manufacturer needs to use desiccants, it would be wise for them to use plastic bags to tightly surround a few boxes at a time, thus limiting the amount of free air space that the desiccant must act upon. If they could pull a vacuum on the bag, they’d have even less moisture left in the void spaces.
Reducing moisture through the use of optimal packaging materials and methods
Many companies don’t realize they are introducing moisture into the system by the types of materials they use. Many Chinese boxes are soft and not very dense and have higher moisture content than materials found in the US. If the shoe manufacturer is using the cheapest possible box material, which not only starts with high moisture content but also absorbs moisture like a sponge as it travels through the distribution system, then they are placing moisture-sensitive products in a moisture-absorbing/producing material.
The same goes for pallets. We have seen a number of times where pallets from Asia produced a tremendous amount of humidity in ocean containers. Replacing wood pallets with plastic slip sheets eliminated the problem, plus allowed more products per container.
The shoe manufacturer may want to consider not using boxes for ocean shipment, along with eliminating pallets (if they were using them). For example, if they shipped each pair of shoes in individually sealed bags with a small amount of desiccant, they’d be able to increase load density by a significant percentage while eliminating the humidity issue. They would need to postpone the packaging operation until the shoes arrive in Panama, but the savings in damages, handling, storage and shipping would pay for having a packaging line in Panama.
Postponing the packaging would also allow the Panama company to provide different SKU’s to different customers, all based on different packages for those specific customers. With the costs of ocean containers continuing to climb, it’s more important than ever for companies to consider ways to densify their products as much as possible, and postponing the packaging is oftentimes a viable way to do just this.
Strategies to Mitigate Mold Growth When the Goods Arrive in Panama?
The biggest problem with mold when goods are in storage in Colon Free Zone is the exceedingly high ambient relative humidity levels in the regions. We have used relative humidity data loggers to validate that levels are consistently in the 75% to 90% range. This is a range where mold will grow extremely fast, causing significant damage to susceptible goods such as leather, fabric shoes.
The best methodology for humidity reduction in Colon warehouses is typically;
- find or create a storage location that can be made airtight to outside air, and moisture. Even small vents, windows, door opening will allow moisture to enter the area that you are trying to manage the moisture
- utilize a commercial grade dehumidification system to reduce the humidity and supplement with air conditioning. The critical success factor is that the dehumidifier be sized appropriately and is the primary system utilized, not the air conditioner.utilize relative humidity data loggers to assure that relative humidity levels stay below the critical 50% level.
Need Help?
Industrial Solutions (Mold Control Panama) provides an engineering service to assess your unique situation. Our engineers will provide a written report of our recommendations and a preliminary budgetary quotation. We represent in Panama the leading United States company for dehumidification systems and can coordinate a turnkey solution for you. COntact us by telephone or WhatsApp +507 6956-1130
###